データ化で顕在化した課題を、いかにうまく改善へつなげるか。見える化の鍵がデータ化なら、改善につなげる鍵は「現場力」だ。
「シンプルなデータなので、現場力が生かされ分析が進みます。さらに、改善した成果がその日の夕方には数字として表れ、正しく評価されることでモチベーションも上がります。
IoTを活用する仕組みづくりで鍵となる人材は、やはり、現場をよく知っている人ですね。さらに、生産技術や情報システム部など他部門の人ともコミュニケーションを取って巻き込んでいけるかどうか。そんな人がいるお客さまはしっかり結果を出されています」(吉原氏)
もう1つ、「小さく始めること」も鍵だという。成果がすぐに見える化され、小さな成功体験を積めることが、次なるアクションへの原動力になるからである。
「『カイゼン』は日本のものづくりの強みですが、本当にカイゼンを推進できている企業は少ないと感じています。その要因の1つとして、日本のものづくりでは多品種少量生産が進んでいることが挙げられます。煩雑な段取りや生産工程に対応するには、見える化の仕組みがないと現状把握すら難しいかもしれません」(吉原氏)
AirGRID®は非常にシンプルな見える化である。その分かりやすさが、社内に浸透しやすく、成果を上げる顧客が多いのだろう。
「これから見える化に取り組む企業では、まず全体を俯瞰できる仕組みの構築が重要だと考えます。今まで見えなかった工場全体の稼働状況や改善すべき課題を発見でき、自動化投資などさまざまなビフォー・アフターが客観的なデータで管理できるからです。
IoTインフラは、これから先どんどん整備されていきます。ビッグデータとシンプルなデータにはそれぞれの特性があるので、目的に合わせてうまく使い分けることで、スピード感あるDX推進が実現できるでしょう」(吉原氏)
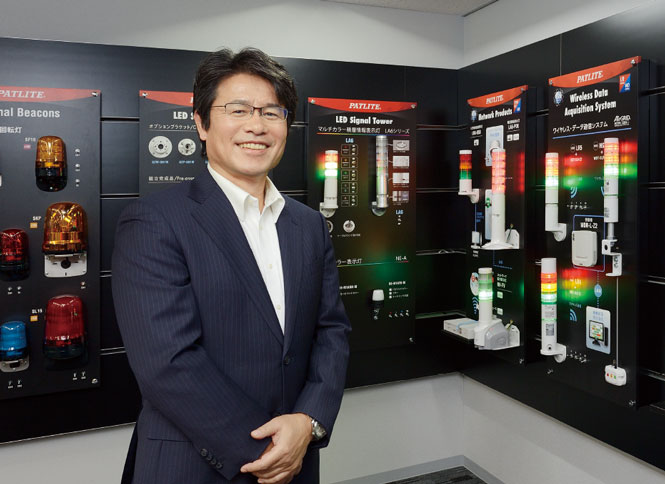
パトライト 営業本部 営業推進課 課長代理 吉原 久雄氏
Column
見える化から「魅せる化」へ
「こんなに簡単な仕組みで、改善が進むんだ……」。パトライトの三田工場を訪れる見学者が、異口同音につぶやく言葉である。三田工場は、3色信号灯のシグナルとAirGRID®によるワイヤレスデータ通信システムを、自動生産機器ではなく、セル生産の組立作業に導入している。
「部品を取りに行く、治具を置き場所へ戻すなど、そのわずか数秒の離席が非稼働時間となります。センシング機能をアドオンして離席情報をデータ化したら、全作業時間の15.6%もありました。顕在化できなかったロスを見える化し、そこから改善が始まったのです」(吉原氏)
2018年に本格的に始動した三田工場の改善プロジェクトは、1カ月で非稼働時間を7.3%(160分)削減するのに成功。3色信号灯を22本生産できる時間が生まれた。また、絶え間ない見学者の存在が「さらに改善して良くしよう!」と、現場の意識も一変させた。製品だけでなく、人やものづくりの仕組み、工場全体で顧客を魅了し、信頼・信用を高めていく。そんな「魅せる化工場」へと、現在進行形で磨きをかけている。
「魅せる化」の工場見学を実施する三田工場
PROFILE
- (株)パトライト
- 所在地:大阪府大阪市中央区久太郎町4-1-3 大阪御堂筋ビル
- 設立:1947年
- 代表者:代表取締役社長 高野 尚登
- 売上高:146億円(連結、2020年3月期)
- 従業員数:1022名(連結、2020年4月現在)